The Rockwell hardness test
method consists of indenting the test material with a
diamond cone or hardened steel ball indenter. The
indenter is forced into the test material under a
preliminary minor load F0 (Fig. 1A) usually 10
kgf. When equilibrium has been reached, an indicating
device, which follows the movements of the indenter and
so responds to changes in depth of penetration of the
indenter is set to a datum position. While the
preliminary minor load is still applied an additional
major load is applied with resulting increase in
penetration (Fig. 1B). When equilibrium has again been
reach, the additional major load is removed but the
preliminary minor load is still maintained. Removal of
the additional major load allows a partial recovery, so
reducing the depth of penetration (Fig. 1C). The
permanent increase in depth of penetration, resulting
from the application and removal of the additional major
load is used to calculate the Rockwell hardness number.
HR =
E - e
F0 =
preliminary minor load in kgf
F1 = additional major load in kgf
F = total load in kgf
e = permanent increase in depth of
penetration due to major load F1 measured in units
of 0.002 mm
E = a constant depending on form of
indenter: 100 units for diamond indenter, 130 units
for steel ball indenter
HR = Rockwell hardness number
D = diameter of steel ball
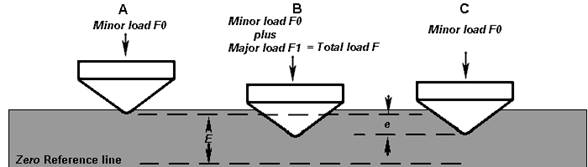
Fig. 1 Rockwell Principle
Rockwell Hardness Scales
Scale |
Indenter |
Minor Load
F0
kgf |
Major Load
F1
kgf |
Total Load
F
kgf |
Value of
E |
A |
Diamond cone |
10 |
50 |
60 |
100 |
B |
1/16" steel ball |
10 |
90 |
100 |
130 |
C |
Diamond cone |
10 |
140 |
150 |
100 |
D |
Diamond cone |
10 |
90 |
100 |
100 |
E |
1/8" steel ball |
10 |
90 |
100 |
130 |
F |
1/16" steel ball |
10 |
50 |
60 |
130 |
G |
1/16" steel ball |
10 |
140 |
150 |
130 |
H |
1/8" steel ball |
10 |
50 |
60 |
130 |
K |
1/8" steel ball |
10 |
140 |
150 |
130 |
L |
1/4" steel ball |
10 |
50 |
60 |
130 |
M |
1/4" steel ball |
10 |
90 |
100 |
130 |
P |
1/4" steel ball |
10 |
140 |
150 |
130 |
R |
1/2" steel ball |
10 |
50 |
60 |
130 |
S |
1/2" steel ball |
10 |
90 |
100 |
130 |
V |
1/2" steel ball |
10 |
140 |
150 |
130 |
Typical Application of Rockwell Hardness
Scales
HRA . . . . Cemented
carbides, thin steel and shallow case hardened steel
HRB . . . . Copper alloys, soft steels, aluminum alloys,
malleable irons, etc.
HRC . . . . Steel, hard cast irons, case hardened steel
and other materials harder than 100 HRB
HRD . . . . Thin steel and medium case hardened steel
and pearlitic malleable iron
HRE . . . . Cast iron, aluminum and magnesium alloys,
bearing metals
HRF . . . . Annealed copper alloys, thin soft sheet
metals
HRG . . . . Phosphor bronze, beryllium copper, malleable
irons HRH . . Aluminum, zinc, lead
HRK . . . . }
HRL . . . . }
HRM . . . .} . . . . Soft bearing metals, plastics and
other very soft materials
HRP . . . . }
HRR . . . . }
HRS . . . . }
HRV . . . . }
Advantages of the Rockwell hardness method include the
direct Rockwell hardness number readout and rapid
testing time. Disadvantages include many arbitrary
non-related scales and possible effects from the
specimen support anvil (try putting a cigarette paper
under a test block and take note of the effect on the
hardness reading! Vickers and Brinell methods don't
suffer from this effect).
|