End Mills
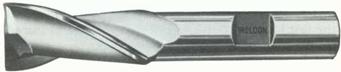
The most frequently
used tool on a vertical milling machine is the end mill.
End mills are made in either a right-hand or a left-hand
cut. Identification is made by viewing the cutter from
the cutting end. A right-hand cutter rotates
counterclockwise. The helix of the flutes can also be
left or right hand; a right-hand helix flute angles
downward to the right when viewed from the side. An
illustration of the cutting end of a four flute end
mill, which is an example of a right-hand cut,
right-hand helix end mill is shown below.
The end teeth of an end
mill can vary, depending on the cutting to be performed.
Two flute end mills are center cutting, which means they
can make their own starting hole. This is called plunge
cutting. Four flute end mills may have either center
cutting teeth or a gashed or center drilled end. End
mills with center drilled or gashed ends cannot be used
to plunge cut their own starting holes. These end mills
only cut with the teeth on their periphery. End mills
can be single end or double end (see table). Double end
type end mills are usually more economical because of
the savings in tool material in their production.
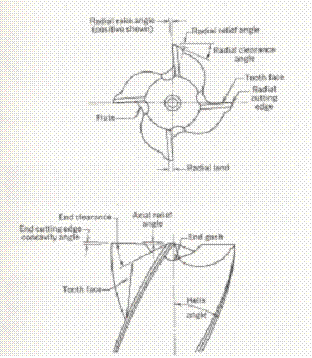
End mills are manufactured with two, three, four, or
more flutes and with straight flutes, slow, regular, and
fast helix angles. A slow helix is approximately
12 degrees, a regular helix is 30 degrees, and the fast
helix is 40 degrees or more when measured from the
cutter axis. Most general purpose cutting is done with a
regular helix angle cutter.
Aluminum is
efficiently machined with a fast helix end mill and
highly polished cutting faces to minimize chip
adherence.
If
large
amounts of material need to be removed, a roughing end
mill should be used. Ball-end end mills have two or
more flutes and form an inside radius or fillet between
surfaces. Ball-end end mills are used in tracer milling
and in die sinking operations. Round bottom grooves can
also be machined with them.
Various End Mills
 |
Standard
Endmill |
 |
Ball Nose
Endmill |
 |
Standard Long
(Length
of flute almost
double
over standard) |
 |
Ball Nose Long
(Length
of flute almost
double
over standard) |
 |
Stub Double-End
Square |
 |
Stub Double-End
Ball |
 |
Aluminum-Cutting |
 |
Rougher/Finisher |
 |
60 Degree Helix |
Micro End Mills
 |
Standard
Decimal Micro Endmill |
 |
Ball Nose
Decimal Micro Endmill |
 |
Standard Long
Reach Micro Endmill |
 |
Ball Nose Long
Reach Micro Endmill
|
 |
Accu-Hold End
Mill Extension Holders |
Burrs
Types
and Characteristics of End Mills
Flutes
- Spiral cutting edge on the end mill. 2 and 4 flute end
mills are the most commonly used.
• 2-Flute - Allows maximum space for chip
ejection. Used for general
milling operations.
• 3-Flute - Excellent for slotting. Used for
general milling operations.
• 4, 5, 6, and 8 Flute - A greater number of
flutes reduces chip load
and can improve surface finish, if feed rate remains the
same.
Ball End
- Used to mill die cavities and fillets, round bottom
holes and slots.
Carbide
- This tool material combines increased stiffness with
the ability to operate at higher SFPM. Carbide tools are
best suited for shops operating newer milling machines
or machines with minimal spindle wear. Rigidity is
critical when using carbide tools. Carbide end mills may
require a premium price over the cobalt end mills, but
they can also be run at speeds 2 1/2 faster than HSS end
mills. For best results mount in a hydraulic type
holder.
Coatings
- The use of Titanium coated tools will increase the
surface hardness of the tool to near 85 Rc. This will
allow for greater tool life at increased cutting speeds
& feeds (15 - 25%). Titanium Nitride (TiN), Aluminum
Titanium Nitride (AlTiN), and Titanium Carbonitride (TiCN).
Cobalt
- Type of high speed steel tool which has a 8% cobalt
content (M42). This material has excellent abrasion
resistance for improved tool life over standard high
speed steel (M7).
Corner Radius
- Conventional end
mill with radius ground on the tips of the flutes to
help reduce chipping on the tip. For mold applications,
radius tools can remove more material faster than ball
ends.
Corner Rounders
- Cutters having form ground radius with relieved
clearance.
Double End
- An end mill that has teeth on both ends of the cutter.
End mill holders must have sufficient clearance to allow
for the use of a double end cutter.
Drill Point
- Multipurpose tool which can be used for drilling,
milling, or chamfering.
High Helix
- Usually a 40 to 60 degree spiral on the tool's flutes.
Effective for rapid chip ejection in milling of aluminum
and other materials.
HSS
- A baseline tool steel. In the past, a majority of end
mills were made from standard High Speed Steel (M7).
Usually inexpensive, but do not offer the tool life or
speed and feed advantages of Cobalt and Carbide end
mills.
Left-Hand Spiral
- Used for milling multiple layers of thin sheets where
chip flow is directed away from work.
Rougher (Hoggers)
- End mill with interrupted shape on outside diameter to
remove large amounts of material quickly. Typically can
remove material up to three times the rate of
conventional end mills with different types available to
achieve the desired finish on the material. Melin offers
roughers in Coarse Pitch, Fine Pitch, Rougher/Finisher,
and 3-Flute for Aluminum styles.
Single End
- Teeth on one end of the cutter only. This style is the
most common available.
Stub Length
- Used for milling of shallow slots in all types of
materials where heavy feeds are required and tool
deflection is minimized.
|